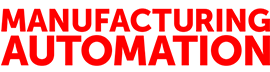
特性操作和管理
自动化3D零件检测作为一个竞争优势
一般检查
一般检查
2016年3月14日–无论制造商追求精益生产、六西格玛还是他们自己的质量保证计划,测量都是质量的核心,也是六西格玛定义测量、分析、改进和控制(DMAIC)生产过程目标的基础。然而,当用传统的手动测量仪和光学比较仪等缓慢的人为主观手段完成测量时,仍会产生多余的浪费,这可能导致生产过程中的无数错误。
使用手动方法,首件检验可能需要45分钟,进货检验审核可能需要数小时,生产件批准流程(PPAP)可能需要数天,精度可能低于预期。
“即使千分尺和卡尺都经过了正确的校准,根据握持、挤压和解读的方式,每个人的测量结果也会有所不同,”螺钉、螺栓制造商Acument Global Technologies北美业务质量副总裁洛基·皮涅罗(Rocky Pinheiro)说。用于汽车、工业、航空航天和国防市场的螺母和冷成型组件。
提供零件二维(2D)或横截面视图的检查设备也不足以满足当今苛刻的质量控制要求。”零件不存在于二维世界中,而存在于三维世界中,”皮涅罗说制造的每个零件都必须在三维空间中与其他部件正确配合并发挥作用。”
由于这些原因,积极主动的制造商正在转向精确、客观的3D在线检测,这种检测可以在手动检测所需时间的一小部分内测量和记录数十个零件特征。这使制造商能够将自动化3D零件检查转化为一种竞争优势,能够显著提高质量和周期时间,减少废品,并将整体设备效率提高20%。
自动三维零件测量
Pinheiro说:“有了LaserLab,我们将在30秒内完成每个零件多达20个三维测量,用于第一部分、每小时和最终检查。”它为我们提供了90%我们想要测量的元素的反馈。从长度、直径、半径和头部高度到拐角、肩部和其他尺寸都非常精确。”
LaserLab是一种三维激光测量系统,可在20秒内测量20多个零件特征,直径可达2微米。General Inspection是一家高速测量和紧固件检查分拣系统的开发商,提供实验室和车间版本。
Pinheiro补充说:“我们看到安装和转换的整体设备效率(OEE)提高了10- 20%,并且使用LaserLab制造部件的速度大大加快。”“我们还大幅减少了首次废料和下游分拣,同时增加了生产周期时间。”
他说,由于激光技术每次测量都具有精确的重复性,通过消除操作员的误差,大大降低了零件之间的可变性。他补充说,一个全面的、内置的螺纹数据库提供了每个螺纹特征的即时公差,每次通过后,激光束都自动校准到NIST标准,以确保准确性。
因此,LaserLab拥有比手动更精确、可重复测量的实时制造过程控制。这允许更频繁的零件测量,显著提高产品质量和减少废料。
根据Pinheiro的说法,Acument Global Technologies以前使用操作员手动检查来确定第一个零件的质量,这需要大约10分钟来检查零件尺寸。
Pinheiro说:“使用3D激光测量系统,我们的检查时间缩短到每个零件不到30秒,节省了20倍的时间。”我们确保我们的工艺在规范范围内运行,因此我们不断生产优质零件。”
3D激光测量系统遵循精益生产和六西格玛的原则,精简了准确的数据收集和统计过程控制(SPC),使科明环球技术处于更好的生产测量、分析、改进和控制的良性循环中。
Pinheiro说:“LaserLab的输出直接以电子方式输入Excel,而不是操作员手工测量零件尺寸并将数据写在纸上输入Excel。”这消除了操作员偏差、错误以及操作员停止测量产品的生产瓶颈,使我们能够以更连续的流程进行制造。”
随着Acument Global Technologies开始在配送中心使用激光实验室进行来料部件识别和验证,Pinheiro预计将看到进一步的好处。该过程将验证正确的部件实际上在容器中。它还将验证关键部件的特征,如长度,直径,平度,角和头部高度。
Pinheiro说:“我们发现,3D激光测量系统(LaserLab)可以将零件识别和验证周期从3-4分钟缩短到20秒左右。“这种效率使得员工可以部署到其他领域,同时确保我们的终端客户的零件质量和准确性。”
虽然该公司的PPAP过程通常需要大约90分钟的时间来测量几个部件的手动量规,如千分尺或卡尺,LaserLab已经节省了大约一个小时的PPAP。Pinheiro说:“这种效率让我的PPAP协调员每个月可以腾出大约一天的时间来进一步加强质量控制。”
据Pinheiro称,与去年相比,Acument Global Technologies也实现了非常强劲的息税前收益(EBITA)表现。他说:“这告诉我,即使我们没有直接测量3D激光测量系统的一些好处,它们也会流向底线。”“任何生产尺寸精度至关重要零件的公司都应该研究3D激光测量系统。我们在一年的时间里就实现了投资回报率,而且仍在实现更高的效率。”
由通用检验公司提供的物品,www.generalinspection.com.
留下一个回复