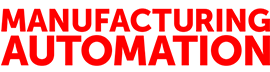
自动化资源特征传感器和愿景
如何选择合适的传感器
由马丁·基南
在制造应用中避免传感器故障的步骤
由马丁·基南
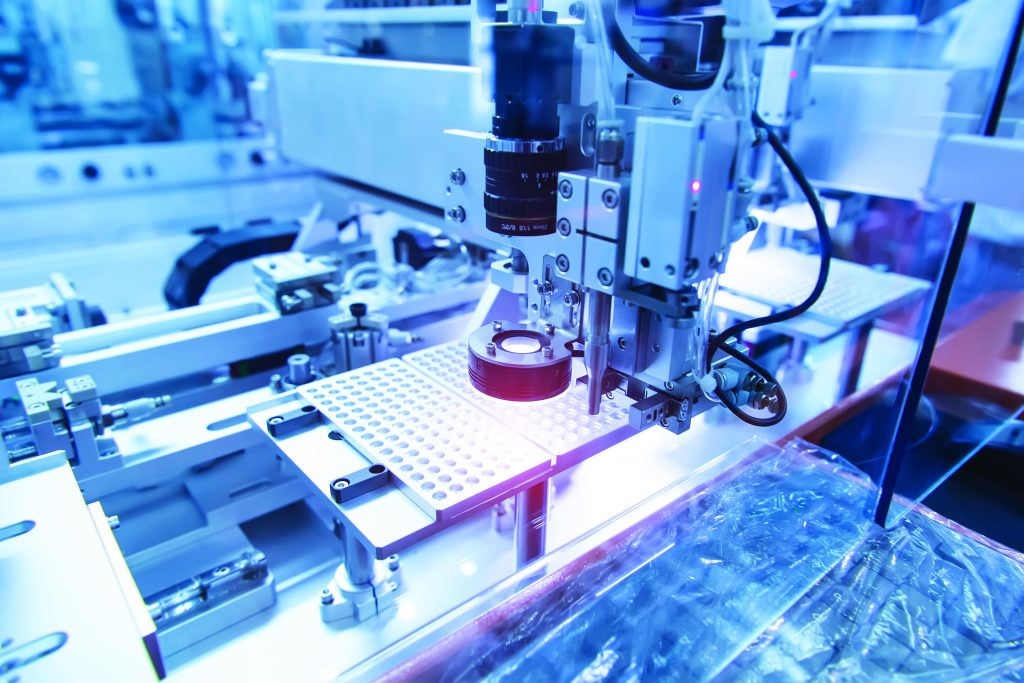
任何工程师都知道,大规模工作会带来一系列特殊的额外开发挑战。一个需要考虑的关键领域是,当传感器在现场出现故障时该怎么办。
有许多常见的缺陷可以落后于传感器故障,并且在本文中,我们将探讨可以遇到的一些最常见的问题,以及可以进行标准化测试过程的广泛适用的方式。
恶劣的环境和传感器特性
正如众所周知的真理所言,有时组件故障实际上是由于一个好的组件在一个糟糕的环境中运行,这可能是最明显的——也是最常见的——故障原因。现代元件和传感器必须在各种各样的条件下工作,在某些情况下,这些条件会迅速从一个极端变化到另一个极端,或在长期使用中加剧。
例如,在加拿大,安装在现代汽车上的传感器可能会经历40摄氏度以上的环境温度、高灰尘和低湿度,几个月内温度会降到零度以下,再加上具有高度腐蚀性的道路盐。
在这种恶劣的环境中,传感器成为首席推动因素以及控制系统中最薄弱的链接,它们是系统中最重要的,但最暴露的部分。因此,通过识别所需的所有重要特征是必不可少的步骤来制定正确的选择。
考虑的特点包括:测量范围,操作的环境条件,可重复性,外形,分辨率,控制界面以及任何特殊要求。
重要的是要记住,传感器只是系统的一部分,所以像Class 1 Division 1这样的连接器和电缆也必须考虑和允许。
传感器建模
这里可以使用的一种技术是传感器建模,它使用数学模型在各种情况下表征传感器行为。确定传感器的传递函数是一个重要的步骤,并且需要在各种条件下观察传感器的标准信号响应。
一旦确定,传感器的传递函数就可以被数据分析模块用作参考模型,它将传感器读数与使用得到的参考模型的预测读数进行比较。
由于一个主要原因,无论是压力传感器还是专用电路中的电容器,任何组件的场故障往往不太常见,那就是老化周期。这个简单的策略显著降低了失败率,因此是测试过程的重要部分。
其背后的逻辑是,有包装、焊接或制造缺陷的组件通常在设备第一次上电的几分钟或几小时内就会失效。在最初几个小时的老化之后,组件故障通常会在底部出现,并且随机发生,直到组件老化开始起作用。
管理变更
组件故障的另一个典型产生因素是更改,而不仅仅是环境更改,而且通常是为了节省成本而产生的更改。一旦设计良好的产品投入生产,成本通常会降低,这意味着量化变更的验证计划是不完整的,这通常会导致灾难。
虽然更好的策略是迭代新的下一代设计而不是改变现有的设计,但对于建造任何更改的完整验证计划至关重要,特别是考虑到下游装配和测试操作。
在许多方面,选择合适的传感器实际上是消除所有错误的选择。一旦设定了应用要求,消除了不符合要求的技术和产品可能是费力的,但最终成功。
快乐狩猎!
Martin Keenan是技术总监Avnet算盘,这有助于和通知设计工程师在技术进步,包括开发应用程序压力传感器,为新产品注入活力。
发表评论