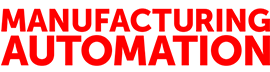
特性工业4.0与智能制造
迈向工业4.0的第一步
作者:Henry Claussnitzer Parker Hannifin
作者:Henry Claussnitzer Parker Hannifin
2016年9月21日消息——工业4.0采用了一系列技术和概念来创建“智能工厂”,在这里,生产过程中的机器能够通过云内部和外部相互沟通。简而言之,工厂、办公室和个人的联网设备将成为智能网络节点,通过标准化网络相互连接,无需任何层级。
更好的过程优化,提高生产力,安全性,可靠性和灵活性,所有业内人业的成功实施都会受到高度重视的结果。革命将导致车间工人和维护人员所需的技能组合的变化,并增加了重要的预测维护量及其准确性。由于流程和系统变得更加可预测可靠,这反过来将产生最小化成本停机的形式的重要回报。
自动化领域的领先公司不仅在整体系统和生产线上增加了传感、数据捕捉和智能,而且还在这些系统中的单个运动控制和自动化设备和产品,无论是机电、气动还是液压。为促进工业4.0而增加的电子硬件和软件,正在模糊电子、液压、气动和Emech技术在工业生产应用中的运动控制之间的界线。
由于所有的生产数据都以数字方式存储在云端,今天的生产管理工具,如工作清单和生产计划,可能仅限于历史书籍。在生产过程中收集的所有数据都可以用于支持数字模型。以一个加工单元为例,这将包括切削速度、进给速度、主轴速度、切削深度、周期时间等参数。这样的数据可能有助于未来的流程改进。可以想象,通过修改云中的数字模型,它还将简化最后一分钟的设计迭代,甚至在按下开始按钮之前的几分钟。
在工业4.0中,连接的机器或设施也可以被视为“信息物理”,这意味着在系统的计算和物理元素之间提供紧密的集成,这也意味着潜在的自主决策。
有各种产品,可以通过互联网来证明如何通过互联网进行通信和互连,用于人机界面(HMI)设计,数据共享/处理和处理支持。虽然没有达到代表行业4.0的乌托邦的完全自主,智能或“学习”生产过程的促进促进,但这些系统正在通过Internet和其他IP网络启用分布式HMI软件,远程支持和应用程序共享。这种类型的能力允许OEM快速而毫不费力地对任何全球位置实施升级和过程更改;它有效地代表了第一个有形步骤进入工业4.0。
除此之外,实际生产的产品将变得“智能”,具有嵌入式系统或智能,提供生命周期监控和客户反馈平台。这是可以实现的,因为数字模型将与物理模型并行存在,跟踪其使用寿命和记录故障,以及其他因素,如维护,寿命结束后的回收,甚至处理。从原材料批号到回收的工厂,所有数据都可以检索。对许多人来说,这种向虚拟世界的转变可能听起来令人生畏,但可能并不比前三次工业革命更可怕,尽管不得不说,随着工业4.0的发展,复杂性有所提高。
当然,对于这种规模的任何新的“转变”,都必须让参与其中的人获得切实的利益。工业4.0承诺微调制造过程,提高效率和灵活性,缩短上市时间,并使定制零件的量产成为可能。如果能够实现这一点,显然将给所有经济体带来巨大的好处。
在竞争激烈的制造景观中,特别是在北美和西欧,通过行业的创新4.0将证明生存的关键。一些政府,如美国,德国和中国的各国政府已经抓住了荨麻,推出了先进的制造计划,以帮助推动将导致联网行业的必要研究和投资。
未来任务的规模是毋庸置疑的。工业4.0是无所不包的,作为一种战略,它不仅受到所谓的物联网(连接物理物体的网络)的影响,还受到摩尔定律等因素的影响,摩尔定律指出,在密集集成电路中,晶体管的数量大约每两年翻一番,显示了计算能力的快速发展。传感器技术是另一个影响因素,大数据分析也是如此。大数据分析是对包含各种数据类型的大型数据集进行检查,以发现隐藏的模式、未知的相关性、市场趋势、客户偏好和其他有用的业务信息的过程。
为了给出特定的制作示例,目前存在各种工具,为工厂管理提供OEE(整体设备有效性)信息,以突出系统的根本原因和系统中可能的故障。相比之下,在一个工厂4.0工厂,组件和系统将能够获得自我意识和自我预测性,从而提供更多关于工厂状态的洞察力的管理。此外,各种组件的对等比较和健康信息的融合将为部件和系统级别提供精确的健康预测,并强制执行工厂管理,以在最佳时间内触发所需的维护,以实现接近零停机时间。
简而言之,工业4.0的目的是通过沟通和智能,使制造业更加灵活、高效和可持续,从而增加竞争力。它将看到要制造的产品包含其生产要求的所有必要信息,便于大规模定制。在这里,通过引入工人在日益复杂的工作中自我优化、自我配置、自我诊断、认知和智能支持的方法,所需的自动化技术得到了改进。此外,考虑到整个价值链,将存在自组织的、集成的生产设施,而灵活的生产决策将基于最新的情况数据。通往工业4.0的道路需要一个集成的、整体的产品规划和生产过程,这将提高生产率、效率和灵活性,其核心是在产品和生产的整个生命周期中建立一个公共数据库和集成工具链。
当然,为了实现这一切,制造商将不得不采用更强大的机器和系统,但扩大IT在其产品中的作用。变化可能包括在云和嵌入式设备上部署更大的功能模块化。
随着工业从今天的通信驱动的自动化发展到明天的创新软件系统对整个生产过程的优化,机器、产品、部件和人之间日益增强的互联性将塑造未来的数字工厂,通过对实际场景虚拟模型的分析,最终达到网络物理系统自优化的目的。
从电机、驱动技术和控制的角度来看,可以看到从昨天的产品包括电机、变速箱、转换器和联轴器,到今天的完全集成的现代自动化世界,再到所有组件与分布式智能的无缝集成。
Henry Claussnitzer是派克汉尼汾工厂自动化集团市场开发经理。
留下一个回复